Photo Etch’s Engineering Department Benefits from SEA Kaizan: Effort Results in Dramatic Work Flow Improvements
FORT WORTH, TX – March 27, 2007 – Photo Etch, a leading aerospace manufacturing company, worked with the Supplier Excellence Alliance (SEA) to implement lean improvements in the company’s engineering department during the week of January 15th. Jonathan Howell, Engineering Manager for Photo Etch and Paul Kobishop, with SEA, led the initiative.
Before implementing the Kaizan, Photo Etch employees who came in contact with the engineering department were interviewed to determine the top three challenges the Kaizan needed to address. During that evaluation process, it was determined that communication between engineers and projects, timeliness and accuracy would be the focus. Shortly after, it was concluded that with less than a 2% inaccuracy rate, the first two priorities – communication and timeliness – were the real issues.
The priorities were addressed as follows:
• |
A unified playbook was created. Information was compiled from the engineers and the best feedback was selected to be part of the playbook. This playbook is now being used to train new engineers and ensure that experienced engineers don’t deviate from the accepted standard. |
• |
Processes were flowcharted. Non-engineering related processes, such as film processing, were eliminated from the engineering department. |
• |
The workload between engineers was balanced. |
• |
The document control clerk’s tasks were increased so engineers could focus on engineering-related activities. |
• |
In the new design process, a manufacturing review step was added to confirm the manufacturability of designs. Manufacturing can also request any necessary tooling or more precise process instructions. |
• |
Stamps for new designs were developed for the machine programmer to avoid delays and confusion. |
• |
Simulation products were given an additional work order so the software programmers can work simultaneously with the engineering department and production time is reduced significantly. |
According to Randy Fry, president and CEO of Photo Etch, “The engineering department Kaizan is simply one example of our commitment to lean manufacturing. We plan to evaluate all key departments to ensure that we are operating with utmost efficiency so our clients get the best products, on time and at the most competitive rates. It’s a win-win effort for us and our clients.”
About Photo Etch
Photo Etch designs and manufactures displays and control panels used for military and commercial airborne and ground communications, as well as navigation systems. The company also manufactures flight simulation and training components. One of Photo Etch’s specialties is night vision technology for airborne military operations. Photo Etch’s client base includes major defense contractors like Boeing, Lockheed-Martin and Grumman Aerospace, as well as U.S. Department of Defense agencies like the U.S. Air Force and U.S. Navy. Founded in 1960, Photo Etch follows ISO 9001 and SAE AS9100 quality standards, as well as a company-wide lean manufacturing initiative. The firm operates from a 50,000-square-foot facility in Fort Worth, Texas. For more information, visit www.photo-etch.com or call (817) 332-3806. |
|
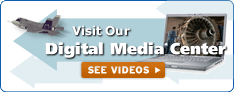
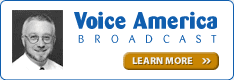
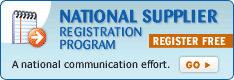 |
|